Application of composite materials to the chenda, an Indian percussion instrument
- Ajith Damodaran , Hossein Mansour , Larry Lessard
- Dec 21, 2013
- 2 min read
An acoustically and structurally effective drum shell is developed for a traditional Indian drum. The basic design concept is a sandwich structure composed of carbon fibre/epoxy face sheet and balsa core on which the drum head is attached. The drum shell structure was fabricated by wet lay-up and a vacuum molding technique. Sound characteristics were analysed for both composite and wooden drums. Measured acoustical performance shows that the frequency response of the composite drum is comparable with that of a traditional wooden drum. It seems promising that composite materials with high damping characteristics could replace wooden structures used in musical instruments. Further, composite manufacturing helps in bringing standardisation and uniformity to musical instrument structures.
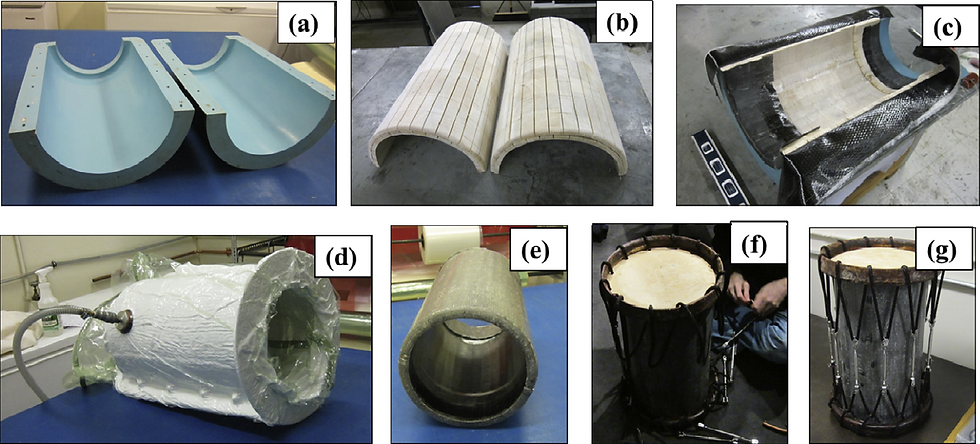
As a result of the interdisciplinary nature of the study, the following conclusions can be drawn in different stages. From the composite manufacturing it was concluded that drum shell structures can be effectively developed by vacuum molding technique. This type of manufacturing would be advantageous in reducing the production time as compared to the traditional wooden instrument. Further, a remarkable weight reduction of 40% was achieved by the composite instrument compared to that of the traditional instrument. Acoustic testing showed that composite and wooden instruments could make comparable instruments. Quantitative evaluation of the percussion instruments was successfully carried out.Quality control can be achieved in the musical instrument industry by the composite manufacturing. It is hoped that this study will assist further efforts in using composite materials for musical instrument structures and other novel applications.

Acknowledgments The assistance of Bruno Paquet, percussionist and Kavish Bujun is gratefully acknowledged. The authors acknowledge the financial support from the Centrefor Interdisciplinary Research in Music Media Technology (CIRMMT) at McGill University and the Department of Foreign affairs and International Trade (DFAIT) Canada. We would like to thank Dr. Iris Bremaud, of CNRS, France for measuring the physical properties of the samples.
Comments